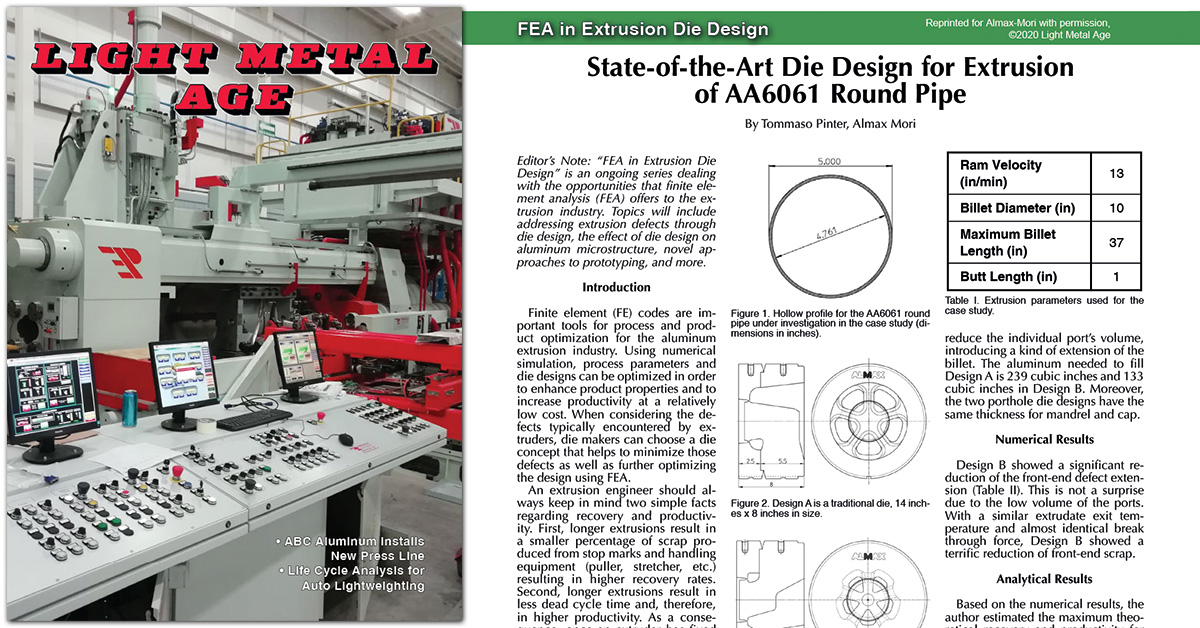
State-of-the-Art Die Design for Extrusion of AA6061 Round Pipe
Abstract
Finite element (FE) codes are important tools for process and product optimization for the aluminum extrusion industry. Using numerical simulation, process parameters and die designs can be optimized in order to enhance product properties and to increase productivity at a relatively low cost. When considering the defects typically encountered by extruders, die makers can choose a die concept that helps to minimize those defects as well as further optimizing the design using FEA. An extrusion engineer should always keep in mind two simple facts regarding recovery and productivity. First, longer extrusions result in a smaller percentage of scrap produced from stop marks and handling equipment (puller, stretcher, etc.) resulting in higher recovery rates. Second, longer extrusions result in less dead cycle time and, therefore, in higher productivity. As a consequence, once an extruder has fixed upon the number of cavities in the die and knows the maximum billet length, they should concentrate on reducing the time required to extrude that length. This can be done by adjusting the alloy, the process and the die. Dies can significantly influence both ram velocity and frontend scrap thus playing an important role in the metal throughput. This fourth article in the series will focus on how, using advanced state-of-the-art die designs, an extruder can significantly improve the quantity of AA6061 saleable pipe produced per single hour of press operation.